The Steps Characteristic for Producing Spunlace Nonwoven Fabric
2017-04-13 15:32:18
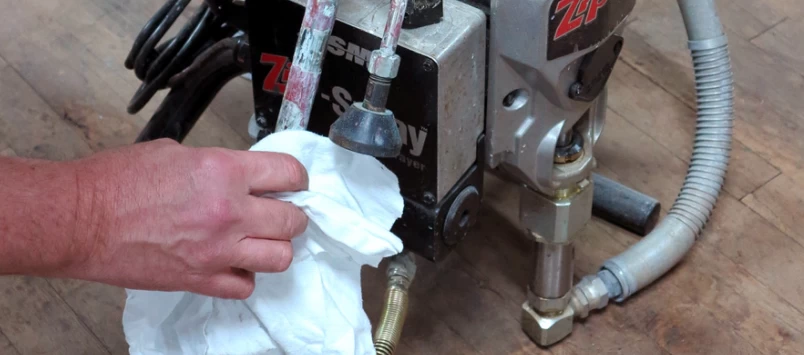
The web which is formed usually by means of air-laid or wet-laid process is initially compressed and then pre-wetted to remove air pockets and then only water-needled. The water pressure usually increases from the first to the last injectors. Generally, there is a thumb rule for pressure, and it is as high as 2200 psi, used to direct the water jets on top of the web. This pressure is more than enough for most of nonwoven fibers, even though higher pressures are also being used in some specialized end use.
The high-pressure jet of water does the entanglement of the fibres in the web. The jets tire out most of the kinetic energy
Primarily in rearranging fibers inside the web.
Secondly, during bounce back against the substrates, dissipating energy to the fibers.
A vacuum inside the roll take out used water from the product, which put a stop to flooding of the product and reduction in the effectiveness of the jets to move the fibers & cause entanglement.
Primarily in rearranging fibers inside the web.
Secondly, during bounce back against the substrates, dissipating energy to the fibers.
A vacuum inside the roll take out used water from the product, which put a stop to flooding of the product and reduction in the effectiveness of the jets to move the fibers & cause entanglement.
Generally, hydro-entanglement is functional on both sides in a stepwise approach. Now the first entanglement roll active on the first side a number of times in order to impart to the web the desired amount of bonding and strength. The web then passes over a second entanglement roll in an overturn direction in order to treat and, thereby, consolidate the other side of the fabric.
The fabric is then passed through a dewatering machine where surplus water is detached and the fabric is dried.